What Is Inside An Electric Car Battery? The Complete Answer
Electric cars are becoming more and more popular every day. This is in part because they don’t rely on gasoline, which means they don’t produce emissions that harm the environment. But many people are still curious about what are electric car batteries made of. In this blog post, we will answer that question and give you a little bit of information about each component of an electric car battery.
Between 300 million and 500 million EVs are expected to be on the road worldwide in the next 20 years. That would be a massive increase from the five million or so new models sold last year. There has been much talk about the promise of environmentally friendly vehicle powertrains in the past, but that time has finally come for passenger cars.
Key Takeaways
- An electric car battery is made up of a combination of individual cells.
- The cells are usually made from lithium-ion, nickel-metal hydride, or lead-acid materials.
- Each type of cell has its pros and cons, with lithium-ion being the most popular. The battery cells are connected in series or parallel to provide more power or a greater range for an electric car.
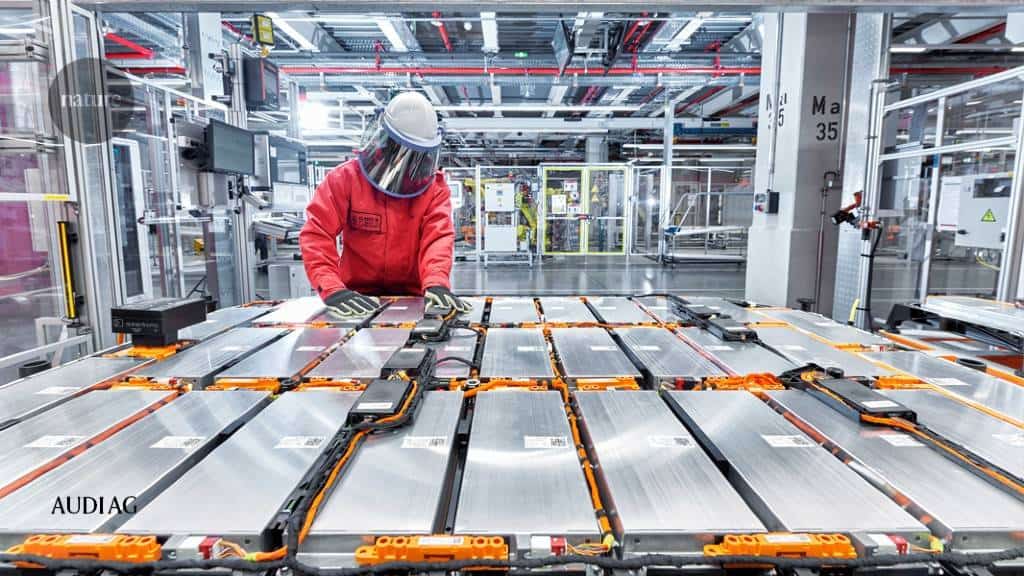
Introduction
A battery is an energy accumulator that stores electricity to be transferred to an alternating or continuous current engine. Batteries are found in electric cars. However, this is only a small portion of its overall significance. The battery is what frees these vehicles from their reliance on fossil fuels and is what gives them their ability to be considered sustainable.
Buyers are most concerned about the following aspects related to batteries: the car’s range, which is defined as the distance that a vehicle can travel before needing a charge; the charging time; and the cost.
The past ten years have witnessed a revolution in the world of batteries on a scale that has never been seen before. As a consequence of this, the typical driving range of electric vehicles has significantly increased, putting an end to the phenomenon known as range anxiety, which refers to the fear that buyers had of becoming stranded on the side of the road due to a lack of driving range. This fear had been preventing sales.
However, the range of batteries is not the only area in which advancements have been made; charging times have also been improved, and rapid charging can now be completed in as little as ten minutes. These changes have improved the batteries’ efficiency as well as their life cycle.
Types of electric car batteries
Lead-acid batteries
Lead-acid batteries are high-power, low-cost, safe, and reliable. However, their limited utility is due to low specific energy, poor performance in cold temperatures, and a short calendar and lifecycle. Although high-tech lead-acid batteries are in development, they are currently only used in electric vehicles with auxiliary loads.
Nickel-metal hydride batteries
Nickel-metal hydride batteries commonly found in IT and healthcare devices have respectable SE and SP ratings. There is a significant difference in the lifespan of nickel-metal hydride batteries and lead-acid batteries, with the former lasting significantly longer.
Battery packs like these have found widespread application in HEVs. Nickel-metal hydride batteries have a number of drawbacks, the most significant of which are their hefty price tag, rapid depletion under load, tendency to overheat, and necessitation for careful hydrogen loss management at high temperatures.
Lithium-ion batteries
Because of their high energy density in comparison to other types of electrical energy storage systems, lithium batteries are currently utilized in the majority of portable consumer electronics.
Examples of this include cell phones and laptops. In addition to this, they have a good capacity to withstand high temperatures, a low rate of self-discharge, a high energy efficiency, and a high power-to-weight ratio.
The majority of the components that make up lithium-ion batteries are recyclable; however, the industry continues to struggle with the high cost of material recovery.
Additionally, the United States Department of Energy is offering the Lithium-Ion Battery Recycling Prize to encourage responsible and profitable solutions for collecting, sorting, storing, and transporting used lithium-ion batteries in order to give them a new life through recycling. This program aims to provide an opportunity for engineers and entrepreneurs alike who are passionate about protecting our environment by promoting sustainability efforts.
An individual or organization that showcases the most innovative and effective solutions will be granted a financial reward. Lithium-ion batteries, which have varying chemical compositions from those of consumer electronics, are used in almost all electric cars and PHEVs these days.
Ongoing research and development efforts are being made in order to bring down their relatively high cost, increase their useful life, and address safety concerns regarding overheating.
Materials used in electric car batteries
Lead-acid batteries: lead, acid (sulfuric acid)
The majority of photovoltaic systems use lead-acid batteries. Lead acid batteries have a low energy density, moderate efficiency, and high maintenance requirements compared to other battery types, but they have a long lifespan and low costs. Because they are the most popular type of rechargeable battery (for example, in starting car engines), lead acid batteries benefit from a well-established, mature technology base, which is one of their unique advantages.
Nickel-metal hydride batteries
Electric cars come with a range of useful features, and the power of their battery is one of the most critical. To ensure that electric vehicles maintain an impressive performance level, materials like nickel and metal hydrides are used to construct their batteries. Not only do they provide good starting energy (SE) and self-discharge (SP) ratings, but these batteries can also last much longer than traditional lead-acid batteries.
In fact, many hybrid electric vehicles (HEV) now utilize nickel-metal hydride packs due to their cost-effectiveness and reliability – making them a great option for drivers looking to get the most from their car’s battery.
Lithium-ion batteries:
Electric cars have revolutionized the way we drive, and that’s thanks to advances in battery technology, specifically lithium-ion batteries.
These batteries use a cocktail of materials including lithium, cobalt, nickel, manganese, and aluminum for the cathode with graphite for the anode. Lithium-ion batteries have a higher energy density than other types of batteries such as lead-acid or nickel-metal hydride batteries, meaning they can remain smaller in size without having to sacrifice storage capacity.
NMC vs LFP (Link to previously written article)
Choosing the right type of lithium-ion battery for your needs can be a tricky task. It’s important to understand the differences between NMC and LFP batteries so that you can select the one that is best suited for your applications. While both use lithium-ion technology, their cathode materials are distinct; NMC is composed of an oxide of lithium, manganese, and cobalt, while LFP uses lithium iron phosphate. Graphite is present in both types.
To gain insights on other specific characteristics and differences between these two battery types, make sure to read an article I put together with more information. After all, it’s always good to have more facts before making an educated decision!
The production process of electric car batteries
Are you interested in the production process of electric car batteries? We’ll take you through it step by step. Here’s the process that goes into making an electric car battery:
Mining and refining of raw materials
The treasures of the earth are unearthed through mining, a process that involves excavating raw materials from deep within its depths. These precious stones or minerals range in abundance – sometimes sitting right on top of the surface and other times hidden beneath layers awaiting discovery by heavy machinery like bulldozers. Once recovered, they’re carried off to processing plants where their inherent values can be brought out with refining techniques.
Mining for natural resources has come a long way, with now multiple methods available to extract different materials. Open pit mining is the most common technique used in surface extraction of minerals, however underground and brine tactics are also utilized – this unique method allows miners to access valuable salts from deep beneath the Earth’s crust.
Choosing the ideal mining method for a particular mineral deposit is essential to extract its valuable resources. After extraction, further processing may be necessary to transform ore and other substances into commodities suitable for use in batteries – making sure these integral materials reach their full potential!
Modern technology has enabled us to make the most of our natural resources by utilizing special extraction techniques. These methods rely on a process that considers each ore’s unique combination of elements, such as solvent extraction, electrowinning, and smelting. With this approach, we are able to unlock valuable materials from their source in an efficient manner.
In an effort to maximize efficiency, various studies are looking for ways to streamline the process of producing battery input materials. The end goal is twofold: save both time and money while creating a solution that would require steps from start to finish.
This can be quite difficult, but once the process is complete and all necessary components have been sourced, battery production can begin. It’s important for us to understand this process in order to better appreciate the effort and hard work that goes into bringing electric vehicles to life.
Manufacturing of battery cells
Once the materials are ready, they’re processed into battery cells by machines. The cells will eventually be assembled into a battery pack, which can be used in cars.
More than 60 percent of all battery capacity in use today is produced in China. Many Chinese companies, including CATL, Funeng Technology, BYD, and Tianjin Lishen, as well as LG Chem and Samsung of South Korea, have opened “mega factories” in China, which are battery manufacturing plants with outputs of at least 20 GWh.
Experts also believe that China will remain the world leader in battery production for the foreseeable future. Companies like Sweden’s Northvolt are contributing to the expectation that Europe will soon surpass the United States as a global leader in battery production within the next decade (whose first factory in Northern Sweden aims at full capacity to produce 32 GWh of capacity per year). We anticipate a 400% increase in global production capacity by 2028.
Key jurisdictions’ legal and regulatory developments will spur investment in battery manufacturing capacity.
For instance, the European Union (EU) has acknowledged the strategic importance of battery manufacturing, and the EU and several Member States, including the United Kingdom (UK), France (France), Germany (Germany), Belgium (Belgium), and the Netherlands (Netherlands), have declared initiatives to promote battery manufacturing.
In order to encourage the production and placement on the EU market of high-performing, safe, sustainable, and durable battery cells, packs, and modules, the EU is currently running a consultation that will end on August 8, 2019, encouraging stakeholders to provide evidence and views on the support for regulatory intervention.
Assembling of battery packs
Battery packs are made up of multiple battery cells wired together and wrapped in protective cases. They are usually mounted inside the vehicle and connected to other electronics. When you connect a charger to your car, it sends power into the battery pack, which then converts it into direct current (DC) electricity that can be used by the vehicle’s electric motors.
These steps in the production process of Electric batteries are quite complex and require a great amount of precision in order to be successful. As companies continue to invest resources into battery production, the industry will evolve and become more efficient over time. With a better understanding of the process, we can all appreciate the hard work that goes into creating electric vehicles and the batteries that power them.
What Are Electric Car Batteries Made Of FAQs
How reliable are electric car batteries?
The technology used in an electric vehicle’s battery has been proven to be reliable over the course of many years. In point of fact, the companies that make EVs guarantee it. For example, Nissan guarantees that the batteries in its electric cars will last for eight years or 100,000 miles, and Tesla provides a guarantee that is comparable to Nissan’s.
What is the future of electric car batteries?
We’ve entered the era of the electric car. Earlier this year, GM, the largest automaker in the United States, announced that it plans to phase out sales of gasoline and diesel vehicles by 2035. German automaker Audi has announced that it will stop making such vehicles after the year 2033. Other auto industry conglomerates have also published long-term plans. The major automakers’ hesitation to electrify their fleets has abruptly turned into a stampede.
It’s possible that even the most optimistic proponents of electrifying personal mobility just a few years ago couldn’t have predicted the current rate of adoption. As a result of government mandates, progress will be made more quickly in many nations. In spite of this, the London-based BloombergNEF (BNEF) consultancy predicts that by 2035, half of all passenger-vehicle sales worldwide will be electric.
According to the International Energy Agency (IEA), this massive industrial transition represents a “shift from a fuel-intensive to a material-intensive energy system”. Massive batteries will be installed in hundreds of millions of vehicles over the next few decades. There will be tens of kilograms of unmined materials in each of those batteries.
There are two major obstacles that materials scientists are attempting to overcome in preparation for a future where electric vehicles predominate. One is how to reduce the use of scarce, expensive, or otherwise problematic metals in battery production due to the high environmental and social costs associated with their mining.
One solution is to make it easier to recycle batteries so that the precious metals in used auto batteries can be put to good use in new ones. Mining engineer and BNEF’s chief metals and mining analyst Kwasi Ampofo predicts that recycling will become increasingly important in the sector.
Where does the material for electric car batteries come from?
Despite China’s dominance in the production of lithium-ion battery packs for electric cars, governments around the world are working to ensure the reliability of their own supply chains as they rush to meet the growing demand for all-electric vehicles.
These batteries currently use components sourced from a select number of countries. In particular, the Democratic Republic of the Congo is responsible for providing half of the world’s cobalt. Indonesia, Australia, and Brazil are all good places to look for a nickel. Meanwhile, Chile, Bolivia, and Argentina account for 75% of the world’s lithium production.
Automakers and battery manufacturers are spending billions of dollars on research to find cheaper production methods and more efficient recycling methods for electric vehicle batteries. The plan is to find ways to recycle used batteries instead of mining them for raw materials to use in making new ones.
Can electric car batteries be repurposed?
Once an electric vehicle’s battery has reached the end of its useful life, it will be recycled. After the standard 8- to 10-year warranty on a battery has expired in the United States, most EV manufacturers and service providers can recycle the batteries for a second or even third time.
The race is on to find ever-better recycling methods to unlock the full green potential of electric cars as they gain market share, reducing greenhouse gas emissions and noise pollution compared to cars powered by fossil fuels.
Can electric car batteries be recycled?
There is more to recycling electric vehicle batteries than preventing them from ending up in dumps.
Having the means to extract the valuable raw elements discovered will eventually cut costs and lessen the need for acquiring more raw materials.
As stated in a report by the American Chemical Society (ACS), “under idealized conditions, retired batteries could supply 60% of cobalt, 53% of lithium, 57% of manganese, and 53% of nickel globally in 2040.” Still, there are obvious hurdles to clear before we get there; recycling electric vehicle batteries is neither simple nor inexpensive.
The Process of Recycling
The raw materials and components that go into making lithium-ion batteries are both hard to come by and highly valuable, even if the battery itself is no longer useful.
However, regardless of whether the battery is shredded, melted, or soaked in acid, the basic principle is the same: the battery is rendered inert to prevent injuries and fires, and the raw materials are extracted from it. The raw materials for new batteries are extracted, processed, and resold.
Recover up to 95% of the raw materials, including cobalt, nickel, and lithium, is the stated goal of most companies that specialize in this process.
While it was possible to provide a simple description of the process of recycling a battery, it is important to note that the actual process is very complex, which is why there are so few companies in the world that do this.
Many automakers working on EVs have wisely announced collaborations with battery recycling firms, because why create something from scratch when it already exists?
Redwood Materials is one company that has teamed up with multiple automakers. With the intention of making electric cars more environmentally friendly and financially accessible, Redwood Materials has formed partnerships with Ford, Toyota, Volkswagen, Audi, and Volvo to collect and recycle their electric vehicles used batteries.
Conclusion
Electric car batteries are essential components of EVs, and the production process involves the mining and refining of raw materials and the manufacturing and assembling of battery cells and packs. We hope this article has given you a better understanding of how electric car batteries are made and why they are so important.
Finally, we have discussed the importance of battery recycling and the process by which batteries are recycled. By doing our part to recycle electric car batteries, we can promote a more sustainable world and reduce the need for new materials in production.